Why Maintenance Matters
Routine maintenance for belt-driven linear guide rails is not optional—it’s essential. Neglect can lead to:
-
Increased friction, wear, and eventual failure
-
Loss of positioning accuracy and throughput
-
Unplanned downtime and costly emergency repairs
-
Safety hazards in serious industrial settings
By following a structured maintenance program, you ensure consistent performance, prolong component life, and reduce total cost of ownership.
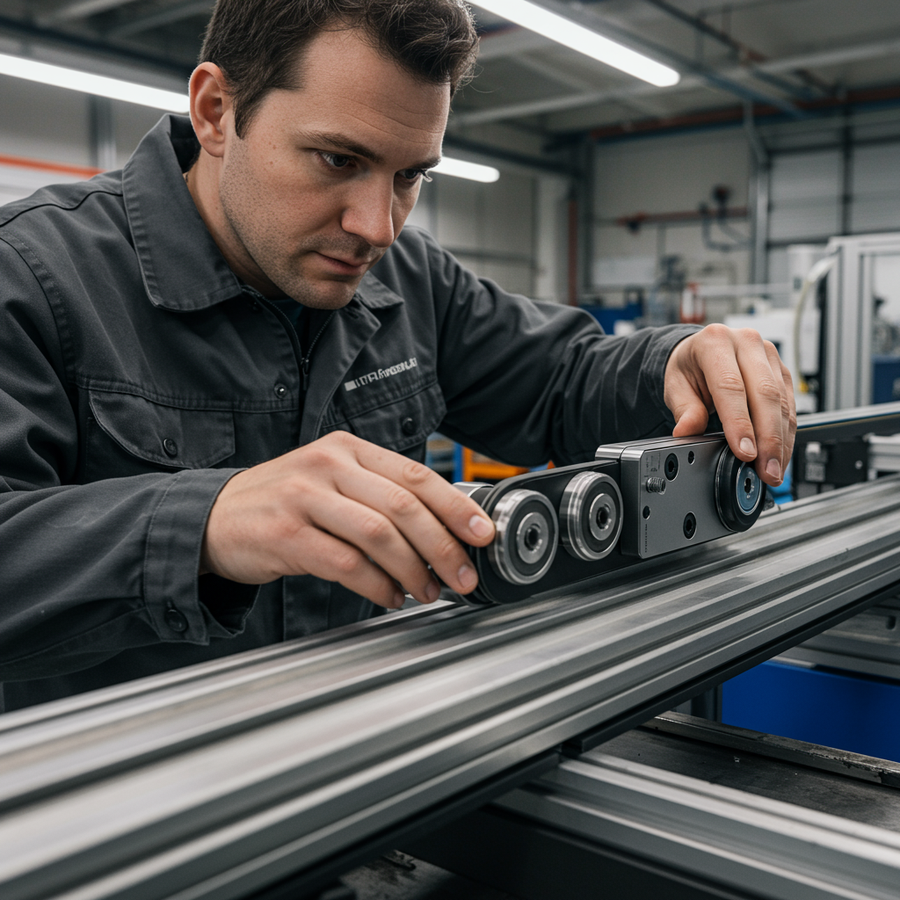
Top 5 Maintenance Tips
1. Proper lubrication
- Clean Before Lubricating: Wipe rails and carriage surfaces with a lint-free cloth. Remove old grease/debris with a suitable solvent if necessary.
- Use Manufacturer-Recommended Lubricant: Typically a lithium-based grease or specific linear-guide oil. Check your actuator’s manual for exact type.
- Apply Correct Amount on Schedule: Aim to lubricate after a set travel distance (e.g., every 50 km of travel) or on a time basis (e.g., monthly/quarterly) depending on duty. Too little lubricant → metal-on-metal wear; too much → dust attraction.
- Method: Use grease nipples (if available) or apply small beads of grease at lubrication points. For oil, use an oil drip system or oil pad designed for CCM linear guides. For oil 30 to 150 cst lubricant depending of model.
- Verification: After lubrication, observe carriage movement—should feel smooth without drag. Maintain records: date, travel hours, lubricant used.
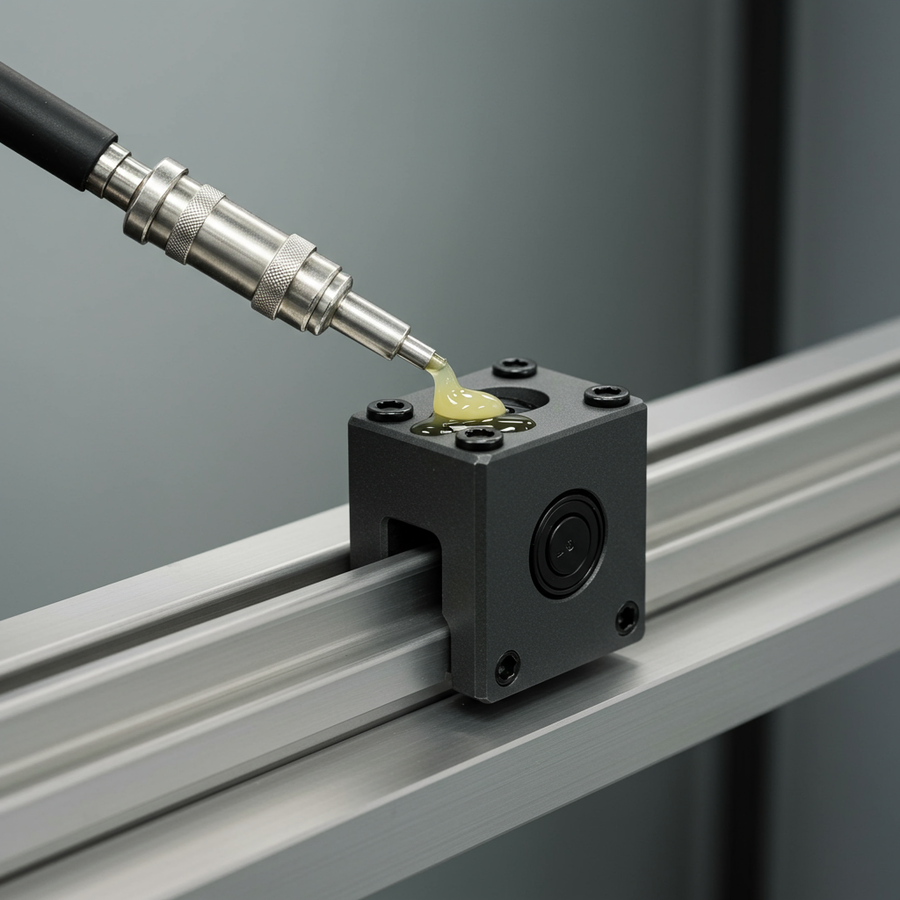
2. Cleanliness And Protection
- Routine Cleaning: Incorporate wiping rails, pulleys, and belt surfaces into weekly or monthly checks. Use lint-free cloths; avoid abrasive tools.
- Shield from Debris: If operating in dusty or wet environments, install wipers, seals, bellows, or covers to keep particulate and contaminants away from rails and belt pulleys.
- Inspect Surroundings: Ensure nearby processes (e.g., material cutting, coolant sprays) are not depositing debris on the rails. Reroute debris or add guards if needed.
- Belt and Pulley Care: Wipe belt teeth and pulley grooves free of dust. Even small particles can abrade belt or pulley surfaces over time, accelerating wear.
3. Belt Tension Check
- Baseline Measurement: At installation, set tension per manufacturer specs. Record force or deflection measurement.
- Periodic Verification: Every few weeks or per recommended interval, use a tension gauge or deflection test (e.g., deflect belt 10 mm, measure force or use frequency method) to check tension remains within specification.
- Adjustment Procedure: Loosen tensioner bolts, adjust until the measured tension matches the spec, then securely lock tensioner.
- Avoid Over-/Under-Tensioning: Over-tensioning stresses bearings and pulleys; under-tensioning leads to backlash, belt tooth wear, and reduced accuracy.
- Document Changes: Keep a log of tension measurements and adjustments. A pattern of frequent loosening may indicate belt stretch or other issues—investigate proactively.
4. Operation Monitoring & Alignment
- Baseline “Feel and Sound”: When system is new or freshly maintained, note normal noise level, vibration, and smoothness.
- Routine Test Runs: At each maintenance interval, run the system through typical motions while observing for:
- Unusual noises (grinding, squeaking)
- Vibration or jerky motion
- Changes in speed or acceleration consistency
- Alignment Checks:
- Ensure rails remain parallel and level. Even slight misalignment can cause one-sided carriage loading.
- Confirm pulleys/idlers and motor sprocket are co-planar: belt should run straight without tracking toward one side.
- Fastener Tightness: Verify that rail-mounting screws, carriage mounting bolts, belt tensioner hardware, and motor couplings remain properly torqued.
- Backlash & Play: Check for increased play in carriage or drive. Excessive play could signal worn bearings or belt stretch.
5. Early Wear Detection & Proactive Replacement
- Visual Inspections: Look for scoring, pitting, corrosion on rails or carriage surfaces. Inspect belt for fraying edges, cracked or missing teeth.
- Debris Indicators: Presence of metal or rubber dust along rails may indicate bearing or belt wear. Investigate source promptly.
- Performance Metrics: Track positioning accuracy over time. Gradual drift may hint at wear in bearings or belt slipping.
- Spare Parts Stock: Maintain an inventory of replacement belts, bearing cartridges, seals, etc., guided by manufacturer’s recommended service life.
- Scheduled Replacement: Plan to replace belts or bearings during planned downtime before end-of-life—prevents sudden failures.
- Record Keeping: Maintain a maintenance log capturing inspection dates, findings, parts replaced, and any anomalies. This data helps predict service intervals and budget for parts.
Pros & Cons of Belt-Driven Linear Guide Maintenance
|
Pros | Cons | |
Accessibility for Maintenance | Belts and rails often easily accessible for inspection and lubrication. | Frequent tension checks may be required compared to screw drives. | |
Cost of Parts | Belts are generally less expensive to replace than ball screws. | Replacement frequency can be higher if environment is harsh. | |
Downtime Impact | Proactive belt replacement is straightforward; no need to disassemble screw assemblies. | Unexpected belt failure can halt operations; vigilance needed. | |
Vibration & Noise | A well-maintained belt drive runs quietly and with less vibration. | Worn belts or misalignment can introduce noise; requires attention. | |
Accuracy Over Time | When properly tensioned and aligned, belt drives offer good repeatability for many applications. | Belt stretch over long service life may degrade accuracy; must monitor. | |
Maintenance Complexity | Basic cleaning, lubrication, and tension checks suffice for many systems. | High-precision or heavy-load applications may need more rigorous monitoring. |
Additional Best Practices
- Environmental Controls: If possible, maintain stable temperature/humidity; extreme conditions can affect lubricant behavior and belt materials.
- Vibration Monitoring: In critical systems, consider adding vibration sensors to detect bearing issues early.
- Training & SOPs: Provide operators and maintenance staff with clear standard operating procedures outlining inspection steps, lubrication methods, and tension-check procedures.
- Use Quality Components: Choose belts, pulleys, rails, and bearings from reputable suppliers; quality parts often have better wear characteristics and clearer maintenance guidelines.
- Integration with CMMS: If you use a computerized maintenance management system, schedule reminders for lubrication, inspections, and part replacements.
- Safety Checks: Always follow lockout/tagout procedures before performing maintenance. Use appropriate PPE when handling lubricants or solvents.
Frequent Answers & Questions
Q1: How often should I lubricate my belt-driven linear guide?
A: It depends on usage and environment. A common guideline is every few weeks to months based on travel distance (e.g., every 50 km of
travel) or operating hours. Always follow your manufacturer’s recommendation and adjust frequency if you observe accelerated wear.
Q2: What lubricant should I use?
A: Use the type specified by your linear guide or actuator maker—often a lithium-based grease for recirculating bearings or a specific linear
guide oil. Using non-recommended lubricants can harm seals or attract excessive debris. If you own a CCM linear guide rail the you can use A 30 to 150 cSt lubricant.
Q3: How do I know if the belt tension is correct?
A: Use a tension gauge or deflection/frequency method per spec. Deflect the belt a set distance (e.g., 10 mm) and measure force or natural
frequency to confirm it falls within the manufacturer’s specified range. If out of range, adjust tensioner.
Q4: My carriage is making noise—what should I check?
A: First, clean and re-lubricate rails; then inspect belt tension and alignment. Check for debris in the carriage bearings or rails, verify
fastener tightness, and observe if pulleys are aligned properly.
Q5: How can I protect linear guides in dusty environments?
A: Install wipers, seals, or bellows to shield rails. Consider using polymer guide options if appropriate. Increase cleaning frequency and
inspect for debris accumulation more often.
Q6: When should I replace the belt?
A: Replace if you observe cracked or missing teeth, frayed edges, or if tension cannot be maintained within spec. Also proactively replace
according to manufacturer’s service life recommendation, even if obvious wear isn’t yet severe.
Q7: Can I automate maintenance reminders?
A: Yes. If you use a maintenance management system, schedule recurring tasks for lubrication, inspection, and replacement intervals. This
reduces risk of forgetting critical upkeep.
More About It
Explore Our Products: Looking for high-quality belt-driven linear guides and accessories? Browse: Our Products.
Contact Our Experts: Need customized advice or support? Reach out for a consultation: Contact Us.
Write a comment