Why selecting the correct belt-driven model matters, performance, wear, lifespan
When it comes to selecting linear motion systems for industrial applications, belt-driven linear guide rails stand out for their speed, flexibility, and ease of maintenance. Whether you're working on a CNC machine, an automated assembly line, or any other industrial motion system, choosing the right linear guide rail is critical to system performance. we’ll walk you through the key considerations, advantages, and expert tips for selecting the perfect belt-driven linear guide rail for your project.
Why Belt-Driven Linear Guide Rails?
Before diving into the specifics of selection, it’s important to understand why you might choose a belt-driven guide rail over other options like ball screws or linear motors. Here are some key benefits:
-
Speed and Long Stroke: Belt-driven systems excel in applications that require high speed and long travel distances. They are ideal for operations that need quick positioning and efficient travel without compromising much on accuracy.
-
Cost-Effective: Belt drives are typically more affordable than ball screw systems, making them an attractive choice for budget-conscious projects that don’t require extreme precision.
-
Maintenance Ease: Unlike ball screws, which often need regular lubrication and can suffer from wear, belt-driven systems are low maintenance and offer longer operational lifespans without frequent servicing.
Key Factors to Consider When Choosing a Belt-Driven Linear Guide Rail
Now that you know why belt-driven rails are a great choice, let’s explore the key factors to keep in mind when selecting the right system.
1. Speed and Load Requirements
-
High Speed: If your application involves long travel lengths or fast speeds (such as in pick-and-place systems, automated assembly lines, or 3D printing, you’ll benefit from the high-speed capabilities of belt-driven actuators. Belt drives offer rapid movements—often up to 2-3 meters per second, making them great for high-speed applications.
-
Load Handling: Though belt-driven rails are great for fast movement, they might not be the best for heavy-duty applications. If your project involves handling large or heavy loads, you may need to combine belts with external support systems or opt for a ball screw for more force.
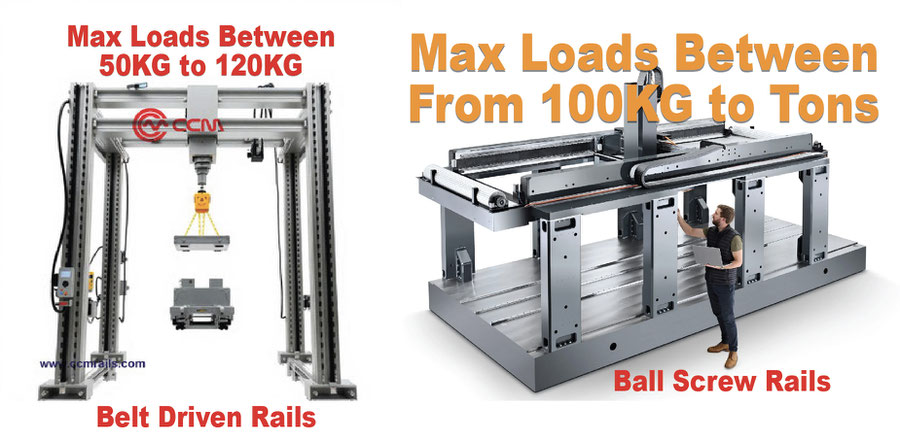
1. Understand the Application and Load Requirements
The first step in choosing the right linear guide rail belt driven system is understanding the application where it will be used. This includes assessing the load that will be carried by the rail, the speed required for the movement, and the overall performance expectations.
Key Factors to Consider:
-
Load Capacity: Determine the weight of the objects that will be moved along the rail. The guide rail must be able to support this load without causing excessive wear or compromising accuracy.
-
Speed and Precision: Consider how fast and precise the movement needs to be. Faster speeds may require higher quality rails to ensure smooth motion, while precision tasks may require tighter tolerances.
Example:
Let’s say you’re designing a CNC machine for milling parts. The machine will move heavy components (up to 50 kg) and requires precise, high-speed movement. For this, you would need a
linear guide rail belt driven system with a higher load capacity, precision tolerance, and smooth, fast operation.
2. Consider the Travel Distance and Stroke Length
Next, consider the travel distance or stroke length — this refers to how far the rail will need to move the carriage. The length of the rail should match the maximum stroke of the equipment to ensure smooth, uninterrupted motion throughout the entire range of movement.
Key Factors to Consider:
-
Custom Stroke Length: If your system requires a custom stroke length, ensure that the guide rail you choose can be manufactured to your specifications.
-
Overtravel: Ensure the rail system can accommodate any overtravel required for your specific application.
Example:
If you need a CNC machine to move a cutting tool over a 2-meter-long workpiece, the linear guide rail belt driven system should support a stroke
length of at least 2 meters to ensure smooth and uninterrupted movement.
3. Evaluate Environmental Conditions
The environment where your linear guide rail belt driven system will operate plays a crucial role in the selection process. Different materials, coatings, and lubrication options can make a significant difference in the system’s performance and longevity, especially if exposed to extreme conditions like dust, moisture, or high temperatures.
Key Factors to Consider:
-
Corrosion Resistance: For systems in harsh environments (e.g., food processing, pharmaceuticals), you may need rails with corrosion-resistant materials or coatings.
-
Temperature and Contamination: Choose a system that can handle the temperature and contamination levels typical for your environment. For example, stainless steel rails are ideal for environments with moisture or chemicals.
Example:
In an industrial setting with high humidity and dust, you might choose a linear guide rail belt driven system with stainless steel rails and
sealed bearings to ensure long-term reliability without corrosion.
4. Precision and Straightness Tolerance
The precision of the linear guide rail belt driven system is crucial for applications that require tight tolerances. A higher degree of straightness tolerance is essential in applications like robotics, optical devices, or CNC machines, where even the slightest misalignment can affect performance.
Key Factors to Consider:
-
Straightness Tolerance: For applications requiring high precision, ensure that the rail system has a low straightness tolerance (e.g., <0.1 mm per meter).
-
Vibration and Shock Resistance: If your system experiences significant vibrations or shocks, look for systems that offer additional resistance to maintain precision.
Example:
For a precision 3D printing machine, you would choose a linear guide rail belt driven system with minimal straightness tolerance, ensuring the
print head moves with high precision for accurate layer deposition.
5. Load Distribution and Carriage Design
Understanding how the load is distributed along the rail and the type of carriage that will be used is critical for ensuring the stability and smoothness of motion. A properly designed carriage ensures that the rail system performs optimally under load.
Key Factors to Consider:
-
Carriage Design: Consider whether you need a single or double carriage for better load distribution.
-
Load Distribution: Choose a model that offers even load distribution across the rail to prevent wear and ensure consistent performance.
Example:
If you’re designing a material handling system for large panels, you may opt for a linear guide rail belt driven system with dual carriages to
better distribute the load and ensure smoother travel across the full stroke length.
Example of How to Choose the Right Model:
Let’s say you’re selecting a linear guide rail belt driven system for a high-precision, high-load CNC machine. The machine will handle a 100 kg load, require a travel distance of 2 meters, and need to move at high speed while maintaining accuracy for intricate cuts.
Here’s how you would select the model:
-
Load Capacity: Choose a system rated for at least 50 kg per rail.
-
Speed and Precision: Opt for a model with a high-speed rating and tight straightness tolerance (e.g., ≤0.05 mm/m).
-
Environment: If the machine will operate in a humid environment, select a stainless steel rail for corrosion resistance.
-
Carriage Design: Choose a dual carriage system for even load distribution.
Based on these criteria, you would likely choose a linear guide rail belt driven system designed for high-speed, high-load applications with stainless steel rails and dual carriages for stability.
Conclusion:
Choosing the right linear guide rail belt driven system doesn’t have to be complicated. By considering your application’s load requirements, travel distance, environmental conditions, precision needs, and carriage design, you can easily narrow down your options and make an informed decision. With the right system in place, you’ll ensure smooth, reliable, and efficient performance for your equipment.
Take the time to evaluate each factor carefully and consult with an expert when necessary. By doing so, you’ll choose the perfect linear guide rail belt driven system to meet your operational needs.
Write a comment